Improving Operational Excellence in Pharma through Effective SOPs
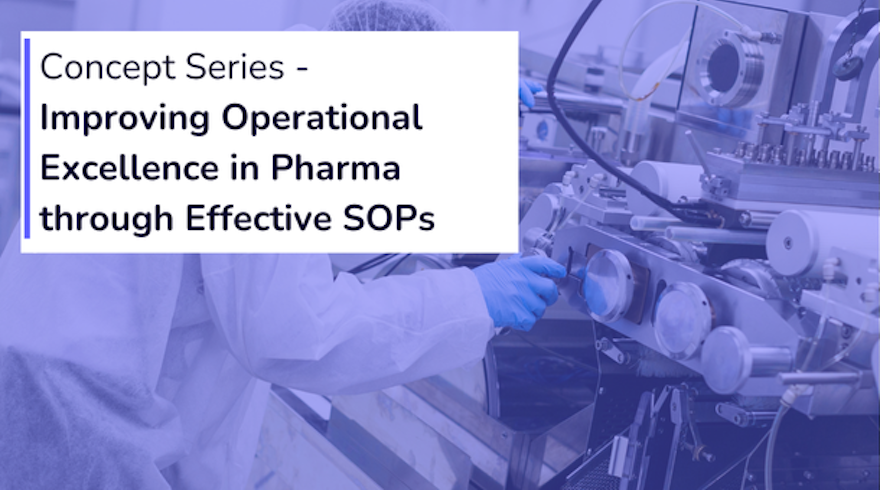
Understanding the Foundation: What Are SOPs in Pharmaceutical Operations?Standard Operating Procedures (SOPs) serve as the backbone of pharmaceutical operations, providing detailed, written instructions that ensure consistent execution of critical processes. In the highl... Read More